Exactly how to Determine What is Porosity in Welding and Improve Your Method
Exactly how to Determine What is Porosity in Welding and Improve Your Method
Blog Article
The Science Behind Porosity: A Comprehensive Overview for Welders and Fabricators
Recognizing the elaborate mechanisms behind porosity in welding is critical for welders and producers striving for remarkable workmanship. From the make-up of the base products to the complexities of the welding process itself, a plethora of variables conspire to either aggravate or ease the existence of porosity.
Comprehending Porosity in Welding
FIRST SENTENCE:
Exam of porosity in welding discloses crucial understandings into the integrity and top quality of the weld joint. Porosity, identified by the existence of dental caries or gaps within the weld steel, is a typical problem in welding processes. These gaps, otherwise correctly resolved, can endanger the structural stability and mechanical properties of the weld, causing possible failings in the completed product.

To detect and evaluate porosity, non-destructive testing techniques such as ultrasonic screening or X-ray inspection are usually used. These strategies enable the recognition of inner problems without endangering the stability of the weld. By analyzing the size, shape, and circulation of porosity within a weld, welders can make informed choices to enhance their welding procedures and achieve sounder weld joints.
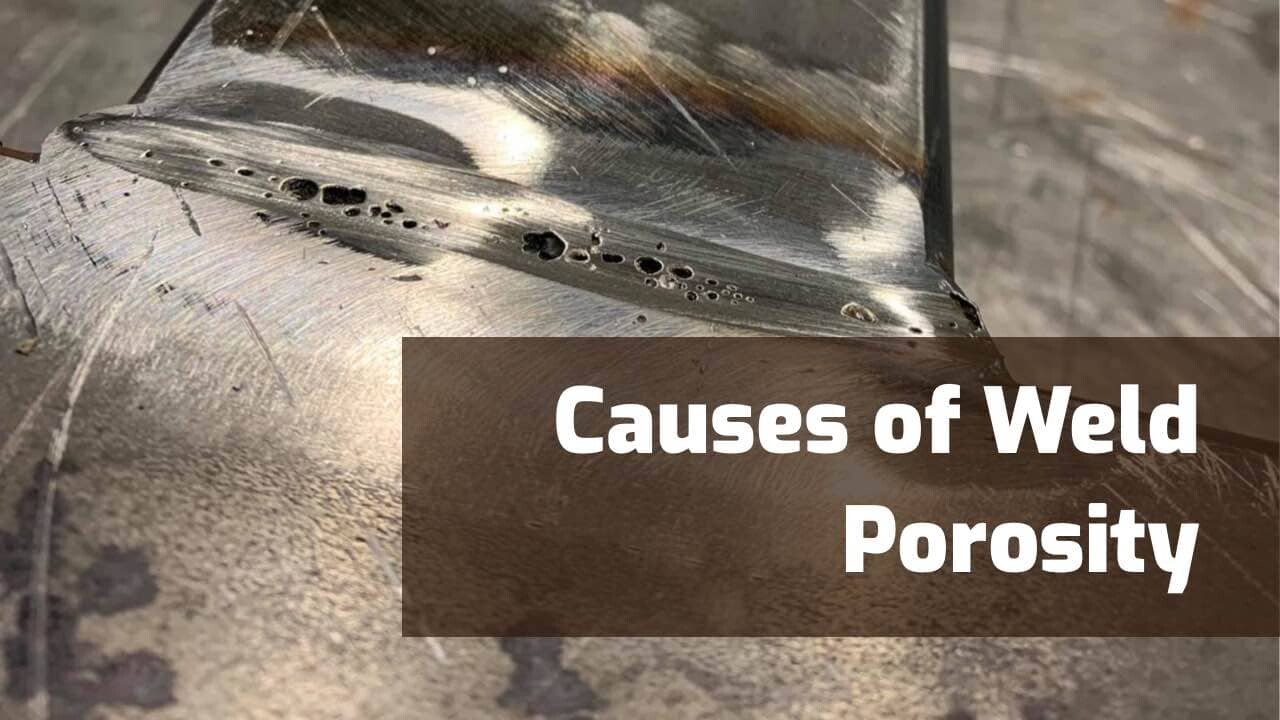
Aspects Influencing Porosity Formation
The incident of porosity in welding is affected by a myriad of aspects, ranging from gas securing performance to the ins and outs of welding criterion setups. Welding criteria, consisting of voltage, present, take a trip rate, and electrode type, likewise influence porosity development. The welding technique utilized, such as gas metal arc welding (GMAW) or protected metal arc welding (SMAW), can influence porosity development due to variations in warmth distribution and gas insurance coverage - What is Porosity.
Results of Porosity on Weld Quality
Porosity formation dramatically jeopardizes the architectural integrity and mechanical homes of bonded joints. When porosity is existing in a weld, it develops voids or tooth cavities within the product, lowering the overall toughness of the joint. These voids work as tension focus factors, making the weld much more susceptible to breaking and failure under tons. The existence of porosity likewise damages the weld's resistance to deterioration, as the trapped air or gases within the gaps can react with the surrounding atmosphere, resulting in degradation gradually. In addition, porosity can prevent the weld's ability to endure stress or influence, more threatening the general top quality and integrity of the welded framework. In check out this site important applications such as aerospace, automotive, or architectural constructions, where safety and sturdiness are critical, the destructive effects of porosity on weld top quality can have extreme consequences, highlighting the relevance of lessening porosity through appropriate welding strategies and treatments.
Methods to Decrease Porosity
In addition, making use of the proper welding criteria, such as the correct voltage, current, and travel speed, is vital in preventing porosity. Preserving a consistent arc size and angle throughout welding also helps reduce the chance of porosity.

Making use of the proper welding technique, such as back-stepping or using a weaving activity, can additionally help disperse heat equally and minimize the possibilities of porosity formation. By carrying out these methods, welders can properly reduce porosity and produce high-quality welded joints.

Advanced Solutions for Porosity Control
Executing sophisticated modern technologies and innovative methods plays a pivotal role in accomplishing premium control over porosity in welding processes. One sophisticated solution is the usage of advanced gas mixes. Securing gases like helium or a mixture of argon and hydrogen can assist reduce porosity by providing much better arc stability and improved gas coverage. Additionally, using sophisticated welding strategies such as pulsed MIG welding or changed environment welding can additionally assist alleviate porosity problems.
One more advanced option entails making use of sophisticated welding tools. Making use of devices with integrated functions like waveform control and innovative power sources can improve weld quality and minimize porosity dangers. In addition, the execution of automated welding systems with accurate control over specifications can substantially minimize porosity defects.
Moreover, integrating sophisticated monitoring and content inspection innovations such as real-time X-ray imaging or automated ultrasonic testing can assist in identifying porosity early in the welding process, permitting prompt corrective actions. Generally, integrating these sophisticated remedies can greatly improve porosity control and boost the total top quality of welded parts.
Verdict
In final thought, understanding the scientific research behind porosity in welding is essential for welders and producers to produce high-quality welds - What is Porosity. Advanced solutions for porosity control can additionally boost the welding process and ensure link a strong and trustworthy weld.
Report this page