What is Porosity in Welding: Usual Sources and Effective Treatments
What is Porosity in Welding: Usual Sources and Effective Treatments
Blog Article
Porosity in Welding: Identifying Common Issues and Implementing Ideal Practices for Avoidance
Porosity in welding is a pervasive issue that commonly goes unnoticed till it creates significant issues with the honesty of welds. In this conversation, we will discover the key elements adding to porosity development, analyze its damaging results on weld efficiency, and go over the best techniques that can be adopted to lessen porosity event in welding procedures.
Typical Reasons For Porosity

Another regular culprit behind porosity is the existence of impurities on the surface of the base steel, such as oil, oil, or corrosion. When these contaminants are not successfully gotten rid of before welding, they can evaporate and end up being entraped in the weld, causing issues. Additionally, making use of filthy or damp filler products can present pollutants into the weld, adding to porosity concerns. To minimize these common root causes of porosity, extensive cleaning of base steels, appropriate shielding gas selection, and adherence to optimal welding parameters are necessary methods in attaining high-quality, porosity-free welds.
Influence of Porosity on Weld Top Quality

The presence of porosity in welding can significantly compromise the structural integrity and mechanical buildings of bonded joints. Porosity creates gaps within the weld metal, compromising its total strength and load-bearing capability.
Welds with high porosity levels tend to exhibit reduced effect strength and minimized capacity to flaw plastically before fracturing. Porosity can hinder the weld's ability to successfully transfer pressures, leading to early weld failing and prospective safety and security dangers in critical structures.
Best Practices for Porosity Prevention
To boost the architectural honesty and top quality of welded joints, what certain actions can be this page executed to reduce the occurrence of porosity throughout the welding procedure? Using the right welding method for the certain product being bonded, such as changing the welding angle and weapon position, can better avoid porosity. Regular examination of welds and prompt removal of any type of issues identified throughout the welding procedure are vital techniques to stop porosity and create high-quality welds.
Significance of Appropriate Welding Techniques
Implementing appropriate welding techniques is extremely important in guaranteeing the architectural honesty and high quality of bonded joints, developing upon the structure of reliable porosity avoidance steps. Too much warm can lead to increased porosity due to the entrapment of gases in the weld pool. In addition, utilizing the ideal welding criteria, such as voltage, current, and take a trip speed, is essential for achieving sound welds with very little porosity.
Additionally, the choice of welding procedure, whether it be MIG, TIG, or stick welding, ought to line up with the certain needs of the task to make sure ideal results. Correct cleaning and prep work of the base steel, as well as picking the best filler material, are also vital parts of efficient welding methods. By sticking to these ideal methods, welders can decrease the danger of porosity development and create high-grade, structurally audio welds.
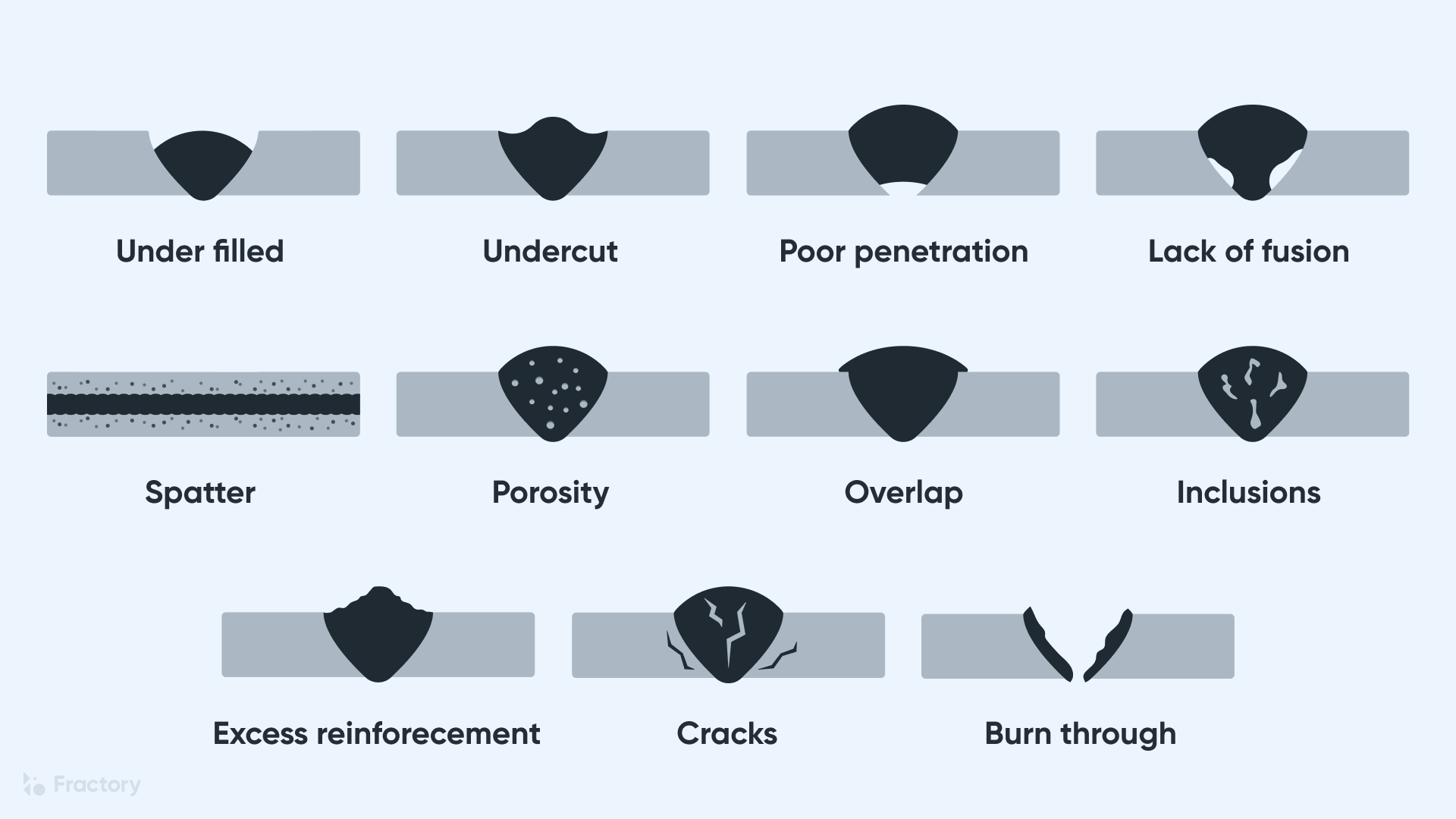
Checking and Quality Control Actions
Evaluating procedures are important to spot and avoid porosity in welding, guaranteeing the toughness and sturdiness of the final product. Non-destructive screening techniques such as ultrasonic testing, radiographic screening, and aesthetic inspection are commonly employed to determine possible issues like porosity.
Post-weld assessments, on Check Out Your URL the other hand, analyze the last weld for any flaws, consisting of porosity, and validate find out here now that it satisfies defined requirements. Executing an extensive high quality control strategy that includes extensive screening procedures and inspections is critical to reducing porosity problems and making certain the general top quality of bonded joints.
Conclusion
To conclude, porosity in welding can be a typical issue that influences the high quality of welds. By recognizing the common root causes of porosity and executing ideal methods for prevention, such as correct welding methods and testing steps, welders can guarantee top quality and dependable welds. It is necessary to focus on avoidance approaches to lessen the occurrence of porosity and preserve the honesty of bonded frameworks.
Report this page